Bild von Michael Schwarzenberger auf Pixabay
In vielen Gewerken ist die wichtigste Ressource nicht unbedingt das Material – sondern die Zeit. Und genau hier trennt sich die Spreu vom Weizen, wenn es um die richtige Ausrüstung geht. Denn veraltete, schlecht gepflegte oder unergonomische Werkzeuge kosten nicht nur Minuten, sondern schnell auch ganze Arbeitstage. Laut Zahlen der BG BAU gehen auf deutschen Baustellen pro Woche im Schnitt rund 38 Minuten je Fachkraft allein für die Organisation oder Suche von Werkzeugen verloren – Zeit, die besser ins Projekt fließen würde.
Dabei ist moderne Ausrüstung weit mehr als ein Kostenfaktor: Sie ist Produktivitätsverstärker, Gesundheitsgarant, Sicherheitsaspekt – und zunehmend auch ein Wettbewerbsfaktor. Wer schneller und präziser arbeitet, kalkuliert sicherer. Wer seine Teams ergonomisch unterstützt, reduziert Ausfälle. Und wer seine Technik intelligent organisiert, schafft Struktur.
Weniger oft bedacht, aber für viele Betriebe dennoch spannend: Auch beim Teambuilding und bei Schulungen kann Ausrüstung zum Thema gemacht werden – zum Beispiel in praxisnahen Settings oder bei Offsites, die zugleich der Weiterbildung und der Ausstattungserprobung dienen.
- Was macht Ausrüstung heute zum Produktivitätsfaktor Nr. 1?
- Welche fünf Kriterien entscheiden bei der Werkzeugwahl wirklich?
- Wie entlastet ergonomische Ausrüstung Körper und Budget zugleich?
- Wann lohnt sich ein Upgrade von analog zu smart?
- Wo spart modulare Aufbewahrung echte Zeit auf der Baustelle?
- Welche Werkzeuge fördert die BG BAU – und warum?
- Wie schlägt sich die richtige Ausrüstung in der Projektkalkulation nieder?
- Wann ist welche Kettensäge sinnvoll – und worauf kommt es wirklich an?
- Wie beeinflusst die Ausrüstung das Miteinander im Team?
- Warum lohnt sich eine Werkzeugstrategie über das Tagesgeschäft hinaus?
- Welche Zukunftstrends bringen 2026+ noch mehr Effizienz?
- Fazit: Drei Schritte zur besseren Ausrüstung – mit System statt Zufall
Was macht Ausrüstung heute zum Produktivitätsfaktor Nr. 1?
Die Auftragsbücher vieler Handwerksbetriebe sind voll – aber der Zeitdruck steigt. Fachkräfte fehlen, Ausschreibungen fordern schnellere Umsetzung, und die Kunden werden anspruchsvoller. In dieser Lage kann schlechte Ausrüstung zum echten Engpass werden. Ob stumpfer Bohrer, schwacher Akku oder instabile Leiter: Wer hier spart, zahlt am Ende doppelt – mit Zeit, Nerven und Folgekosten.
Immer mehr Betriebe stellen daher ihre Werkzeugstrategie auf den Prüfstand. Denn die Erkenntnis setzt sich durch: Gutes Werkzeug macht nicht nur bessere Arbeit möglich, es macht sie oft auch messbar schneller.
Zahlen, die aufhorchen lassen
Eine aktuelle Analyse der BG BAU zeigt: Fehlende oder nicht funktionstüchtige Werkzeuge führen im Schnitt zu rund 16 % Zeitverlust pro Arbeitstag. Hinzu kommen die Risiken durch Improvisationen – etwa bei unpassender Hebetechnik oder fehlendem Schutz. Die Zahl der meldepflichtigen Muskel-Skelett-Verletzungen liegt in Bau- und Ausbaugewerken konstant auf hohem Niveau. Auch das ist eine Folge falscher Ausrüstungsentscheidungen.
Welche fünf Kriterien entscheiden bei der Werkzeugwahl wirklich?
Wer einmal mehr ausgibt, hat oft länger Ruhe. Klingt banal – ist aber im Arbeitsalltag oft entscheidend. Dennoch ist nicht jedes teure Gerät automatisch besser. Fünf Kriterien helfen, bei der Auswahl die richtigen Prioritäten zu setzen.
Diese fünf Punkte sollten nie fehlen:
- Lebensdauer: Wie robust ist das Werkzeug wirklich? Prüfzertifikate, Belastungstests und Rückgaberegelungen geben erste Hinweise.
- Ergonomie: Ist das Gerät auf Dauerbelastung ausgelegt? Wie hoch ist das Gewicht bei Überkopfarbeiten?
- Modularität: Passt das neue Gerät zu bestehender Ausrüstung? Sind Akkus, Koffer oder Bits systemkompatibel?
- Energieeffizienz: Gerade bei Akku-Geräten zählt jede Wattstunde – auch mit Blick auf Nachhaltigkeit.
- Digitale Integration: Smartes Tracking, Fehlerdiagnose oder Ladezyklenüberwachung machen Geräteflotten planbarer.
Doch damit ist es nicht getan. Auch die vermeintlich beste Ausrüstung bringt wenig, wenn sie im Alltag nicht sinnvoll eingesetzt wird. Ein Bohrhammer mit digitaler Schlagkraftkontrolle nützt wenig, wenn er in der falschen Box liegt oder ständig mit leeren Akkus am Einsatzort ankommt. Deshalb lohnt sich der Blick über das einzelne Gerät hinaus – hin zum Zusammenspiel aller Komponenten.
Denn: Gute Ausrüstung ist immer Teil eines Systems. Wer Werkzeug, Aufbewahrung, Energieversorgung und Wartung nicht als Einheit denkt, schafft sich unnötige Reibungspunkte. Gleichzeitig wird klar: Die besten Lösungen sind nicht zwangsläufig die teuersten – sondern die, die zur eigenen Arbeitsweise passen.
Was wird wirklich gebraucht?
Welche Werkzeuge werden am häufigsten genutzt, wo kommt es regelmäßig zu Ausfällen, und welche Geräte sind schlicht nicht mehr zeitgemäß? Gerade bei Elektrowerkzeugen lohnt sich ein genauer Blick: Sind ältere kabelgebundene Geräte noch praktikabel oder behindern sie inzwischen den Arbeitsfluss? Wer etwa regelmäßig mit Holz arbeitet, sollte auch prüfen, ob eine moderne Akku-Variante nicht die bessere Wahl wäre – etwa durch geringeres Gewicht, weniger Lärm und mehr Flexibilität. Einen aktuellen Überblick bieten entsprechende Plattformen: Wer sich beispielsweise Akku-Kettensägen im Vergleich ansieht, kann die eigene Ausstattung realistisch einordnen – und gezielt modernisieren, wo es sinnvoll ist.
Die fünf Kardinalfehler beim Ausrüstungs-Kauf
- Schnäppchenjägerei ohne Langzeittest
→ Billig heißt oft: keine Ersatzteile, keine Garantie, keine Präzision. - Geräte ohne Plattformbezug kaufen
→ Wer beim Hersteller-Mix keine Strategie hat, zahlt bei Akkus und Ladegeräten drauf. - Ergonomie unterschätzen
→ Jedes zusätzliche Kilo am Handgelenk macht sich nach drei Stunden bemerkbar. - Schutzfunktionen ignorieren
→ Abschalt-Automatik, Kettenschutz oder Vibrationsdämpfung sind kein Luxus, sondern Sicherheit. - Transport und Aufbewahrung nicht mitdenken
→ Wer täglich 15 Minuten mit Suchen verbringt, verliert auf ein Jahr gerechnet fast 7 volle Arbeitstage.
Wie entlastet ergonomische Ausrüstung Körper und Budget zugleich?
Laut aktueller Auswertung der Deutschen Gesetzlichen Unfallversicherung (DGUV) gehen rund 29 % aller meldepflichtigen Arbeitsunfälle im Baugewerbe direkt oder indirekt auf körperliche Überlastungen zurück. Das sind nicht nur abstrakte Prozentwerte, sondern Tausende Krankmeldungen pro Jahr – jede einzelne mit Kosten für Betrieb und Sozialkassen. Die Palette reicht von hartnäckigen Rückenschmerzen nach ständigem Bücken bis zu chronischen Schulterbeschwerden durch Überkopfarbeiten. Hinzu kommen Mikrotraumata an Hand- und Ellenbogengelenken, die oft erst spät erkannt werden, dann aber lange Ausfallzeiten nach sich ziehen.
Dabei ist die technische Lösungsszene inzwischen breit aufgestellt: höhenverstellbare Werkbänke, rückenschonende Rucksäcke für mobile Energieversorgung, vibrationsgedämpfte Maschinen sowie Akkuschrauber mit kraftsparender Drehmomentregelung senken die tägliche Belastung spürbar. Trotzdem klafft in vielen Betrieben eine Lücke. Warum? Häufig fehlt das Bewusstsein, wie eng Arbeitsgesundheit und Geräteeinsatz zusammenhängen. Sobald aber klar ist, dass jeder unnötige Kraftakt eine potenzielle Krankmeldung bedeutet, ändert sich meist auch die Investitionsbereitschaft.
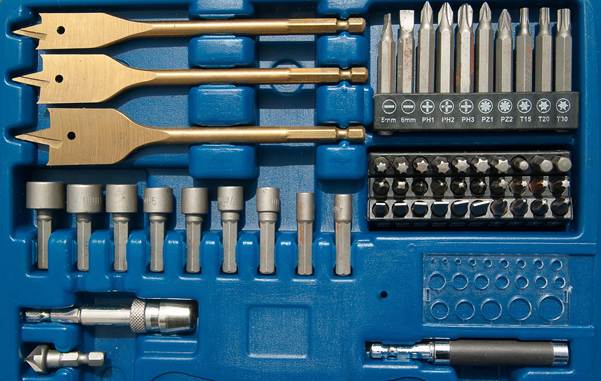
Sechs Hebel für sofort spürbare Entlastung
- Gewicht reduzieren: Leichtere Gehäusematerialien oder kabellose Geräte verringern Zug- und Druckbelastungen.
- Vibrationen dämpfen: Anti-Vibrations-Griffe und entkoppelte Motoren schützen Gelenke und Nervenbahnen.
- Arbeitshöhe anpassen: Mobile Hebe- und Werkbanksysteme sorgen für geraden Rücken statt Dauerkrümmung.
- Griffzonen optimieren: Ergonomisch geformte Griffe verteilen die Kraft gleichmäßiger, besonders bei Dauergriffen.
- Akku-Plattformen vereinheitlichen: Weniger Akkutausch spart Griffwechsel und Fehlbelastungen.
- Schulungen einplanen: Kurze Ergonomie-Briefings verankern die korrekte Körperhaltung im Alltag.
Ergonomie rechnet sich – nicht nur medizinisch
Rechnet sich das? Ein mittelständischer Dachdeckerbetrieb konnte durch Umstieg auf vibrationsarme Maschinen und höhenverstellbare Böcke die krankheitsbedingten Fehlzeiten von zwölf auf acht Tage pro Beschäftigtem und Jahr senken. Allein die geringeren Lohnfortzahlungen deckten binnen 18 Monaten die Investitionskosten – ganz abgesehen von der höheren Arbeitsmotivation, weil sichtbare Wertschätzung spürbar wirkt.
Wann lohnt sich ein Upgrade von analog zu smart?
Die Digitalisierung macht vor der Baustelle nicht halt. Doch Smart Tools sind kein Selbstzweck, sondern sollen Prozesse vereinfachen. Bluetooth-fähige Bohrhämmer, Ortungschips in Werkzeugkoffern oder App-gesteuerte Ladegerätesind nur drei Beispiele, die zeigen, wohin die Reise geht. Mit einer Sensor-Box in der Akkuaufnahme wird etwa jede Lade- und Entladekurve dokumentiert. Das klingt zunächst nach Spielerei, reduziert in der Praxis aber Totalausfälle, weil schwächelnde Energiespeicher früh erkannt werden.
Smart-fähige Geräte zahlen besonders dort ein, wo mehrere Teams zeitgleich auf dieselbe Ausrüstung zugreifen. In Echtzeit lässt sich nachvollziehen, wer welches Gerät nutzt, wann es das letzte Mal gewartet wurde und ob Ersatzteile fällig sind. Das minimiert Leerlauf, weil kein Team mehr lange sucht oder überrascht in der Werkstatt steht. Ebenso wichtig: automatisierte Wartungsprotokolle. Statt händischer Einträge meldet das Gerät seine Stundenzahl selbst – spätestens dann, wenn der nächste Schmier- oder Filterwechsel ansteht. Ersatzteile können frühzeitig bestellt werden, Ausfälle schrumpfen auf ein Minimum.
Vier Fragen, mit denen sich ein Smart-Upgrade schnell rechtfertigen lässt
- Wie oft gehen Geräte „verloren“ oder bleiben unauffindbar? Digitale Ortung holt pro Monat im Schnitt zwei Arbeitsstunden zurück.
- Wieviel Zeit kostet ungeplante Wartung? Predictive-Maintenance-Funktionen senken Spontanreparaturen oft um ein Drittel.
- Sind unterschiedliche Akku-Systeme im Umlauf? Eine Plattform spart Ladegeräte, Transporte – und Nerven.
- Wie hoch sind derzeitige Ersatzteil- und Reparaturkosten? Transparente Nutzungsdaten erleichtern die Budgetplanung merklich.
Dass Smart-Tools in der Anschaffung teurer sind, ist unbestritten. Entscheidend ist der Blick auf die Gesamtkosten über Lebenszeit. Eine fünfjährige TCO-Analyse eines Trockenbauers zeigt, dass sich der Mehrpreis bereits nach zweieinhalb Jahren amortisiert hat – allein durch geringere Stillstände und längere Gerätelebensdauer.
Vorteile für Planung und Ersatzteilmanagement
Gerade bei mehreren Teams oder wechselnden Einsatzorten bringt smartes Equipment Struktur: Wer welches Gerät wann nutzt, wie lange, mit welchem Verschleiß – das lässt sich mit digitaler Verwaltung klarer steuern. Fehlercodes werden per App ausgelesen, Wartungszyklen vorab gemeldet, Ersatzteilbestellungen automatisiert.
Zugegeben: Die Einstiegskosten sind höher. Doch wer über die Laufzeit rechnet, profitiert von weniger Ausfällen, besserer Kontrolle und transparenter Planung. Und: Einige Systeme lassen sich nachrüsten – z. B. durch Tracking-Chips oder vernetzte Akkus.
Wo spart modulare Aufbewahrung echte Zeit auf der Baustelle?
Kaum ein Tag vergeht, an dem nicht irgendwo auf der Baustelle nach einem Bit, Akku oder Spezialaufsatz gesucht wird. Jedes Teil findet sich schließlich wieder, doch die Summe der Suchzeiten ist enorm. Module, die sich stapeln, verriegeln und rollen lassen, sind deshalb längst Standard bei großen Bauunternehmen. Kleinere Betriebe hingegen zögern noch, weil die Anschaffungskosten zunächst über den klassischen Baumarkt-Kofferpreisen liegen.
Trotzdem lohnt sich der Blick aufs Detail: In modularen Boxen ist nicht nur alles schnell greifbar; sie lassen sich auch fahrzeugseitig sichern, sodass nichts verrutscht oder beschädigt wird. RFID- oder Bluetooth-Tags melden sogar, wenn ein Teil fehlt – praktisch, wenn Teams parallel in unterschiedlichen Stockwerken arbeiten.
Kurze Feldstudien zeigen: Ein Zwei-Mann-Team spart mit konsequentem Modulsystem im Vergleich zu herkömmlichen Koffern durchschnittlich 12 Minuten pro Tag. Hochgerechnet auf 220 Arbeitstage sind das über 44 Stunden – mehr als eine ganze Arbeitswoche, die sich produktiver nutzen lässt. Dazu kommt der Sicherheitsaspekt: Weniger loses Material bedeutet weniger Stolperstellen, weniger Beschädigungen und letztlich geringere Reparaturkosten.
Auch in puncto Nachhaltigkeit haben modulare Systeme Vorteile. Statt immer neue Koffer zu kaufen, lassen sich defekte Deckel oder Rollen einfach austauschen. Einige Hersteller bieten zudem Recycling-Programme an: Gebrauchte Module werden zurückgenommen, Kunststoff und Metall fachgerecht getrennt und wiederverwendet. So schont das System nicht nur Zeit und Geld, sondern auch Ressourcen – ein Argument, das bei öffentlichen Ausschreibungen zunehmend gefragt ist.
Welche Werkzeuge fördert die BG BAU – und warum?
Gute Ausrüstung ist mehr als eine Frage der Effizienz – sie kann auch Sicherheit gewährleisten und die körperliche Belastung verringern. Genau hier setzt die BG BAU mit ihren Förderprogrammen an. Ziel ist es, Betriebe zu unterstützen, die in ergonomische oder sicherheitsrelevante Ausstattung investieren. Dahinter steckt eine klare Rechnung: Jeder verhinderte Ausfalltag, jeder vermiedene Unfall bedeutet weniger Kosten – nicht nur für die Betriebe, sondern auch für die Versicherungssysteme.
Gefördert werden unter anderem vibrationsarme Maschinen, Tragehilfen für schwere Materialien, klappbare Arbeitsplattformen oder Absaugsysteme gegen Feinstaub. Auch hochwertige persönliche Schutzausrüstung fällt darunter. Die Förderung ist in der Regel an konkrete Produkte und Voraussetzungen gebunden – sie muss vor dem Kauf beantragt werden und setzt eine ordentliche Dokumentation voraus.
Wer sich frühzeitig informiert und die Anträge sauber vorbereitet, kann sich bis zu 50 Prozent der Investitionskosten zurückholen. Und spart damit nicht nur Geld, sondern schafft auch intern ein klares Signal: Gesundheit und Sicherheit haben Priorität. Viele Betriebe nutzen die Gelegenheit übrigens, um im Zuge der Förderung gleich ihre gesamte Werkzeugstrategie neu zu denken – etwa im Rahmen von Jahresplanungen oder bei Generationswechseln im Unternehmen.
Wie schlägt sich die richtige Ausrüstung in der Projektkalkulation nieder?
Manchmal lässt sich Produktivität auf die Minute herunterbrechen. Und genau das wird in der Projektkalkulation zunehmend relevant. Denn jedes unnötige Umrüsten, jeder Ausfall wegen verschlissener Technik, jeder improvisierte Ersatz kostet nicht nur Zeit, sondern verzerrt auch die Kalkulationsgrundlage.
Ein konkretes Beispiel: Ein Betrieb ersetzt seine veralteten Bohrhämmer durch neue, leichter zu führende Geräte mit höherer Akkuleistung. Ergebnis: Zwei Arbeitsschritte weniger, geringerer Kraftaufwand – und eine spürbar schnellere Taktung. Über den Zeitraum eines Jahres summiert sich das auf mehrere volle Arbeitstage, die anderweitig genutzt werden können.
Was sich abstrakt anhört, wird in der Praxis schnell spürbar. Viele Unternehmer berichten, dass sich eine durchdachte Ausrüstungsmodernisierung bereits nach einem einzigen größeren Auftrag rechnet – vor allem, wenn dadurch Personalengpässe besser kompensiert oder Zusatzarbeiten schneller übernommen werden können.
Ein weiterer Aspekt: Neue Ausrüstung wirkt sich auch auf die Außenwirkung aus. Wer mit gepflegtem, modernem Werkzeug zum Kunden kommt, sendet automatisch ein Signal von Professionalität und Qualität. Und das wiederum beeinflusst die Preisdurchsetzung – eine Variable, die oft unterschätzt wird.
Wann ist welche Kettensäge sinnvoll – und worauf kommt es wirklich an?
Kettensägen sind ein Werkzeug mit vielen Gesichtern: Im Garten- und Landschaftsbau gehören sie genauso zum Alltag wie bei Zimmerern oder Sanierern. Doch nicht jede Säge passt zu jedem Zweck – und längst nicht jede muss mit Benzin betrieben werden.
Benzin-Kettensägen bieten weiterhin die höchste Leistung, sind aber laut, wartungsintensiv und stoßen Emissionen aus. Kabelgebundene Modelle liefern gleichmäßige Leistung, sind aber ortsgebunden. Deutlich an Bedeutung gewinnen inzwischen Akku-Kettensägen: Sie sind leise, leicht, sofort startklar und wartungsarm – ideale Begleiter für kleinere Baustellen, den urbanen Einsatz oder Tätigkeiten in lärmsensiblen Umgebungen.
Gerade für Handwerksbetriebe, die flexibel und effizient arbeiten wollen, lohnt sich ein genauer Blick auf die aktuellen Modelle. Oft wird dabei auch klar: Wer einmal bewusst auswählt, statt zu improvisieren, reduziert nicht nur Verletzungsrisiken, sondern spart langfristig auch Zeit. Denn funktionierende, passende Geräte führen zu weniger Unterbrechungen – und das zahlt sich unmittelbar aus.
Wie beeinflusst die Ausrüstung das Miteinander im Team?
Technik ist nicht nur ein Mittel zum Zweck – sie wirkt sich auch auf das Arbeitsklima aus. In vielen Handwerksbetrieben entsteht Frust genau dort, wo Werkzeuge fehlen, unauffindbar sind oder schlecht gewartet wurden. Wenn sich Teams regelmäßig mit leeren Akkus, stumpfen Sägeblättern oder zu wenigen Maschinen herumschlagen müssen, sinkt die Arbeitsmoral – ganz unabhängig vom handwerklichen Können.
Umgekehrt zeigt die Praxis: Betriebe mit durchdachter Werkzeuglogistik, klarer Zuständigkeit und moderner Ausstattung erleben seltener Reibungsverluste im Alltag. Wer weiß, dass die Technik funktioniert und verfügbar ist, kann sich auf die eigentliche Arbeit konzentrieren – das senkt Konfliktpotenziale, spart Zeit und erhöht die Identifikation mit dem Unternehmen.
Besonders relevant wird dieser Zusammenhang bei der Einarbeitung neuer Mitarbeiter oder Auszubildender. Ein professioneller Maschinenpark vermittelt Wertschätzung und Strukturbewusstsein. Neue Teammitglieder orientieren sich schneller, arbeiten sicherer und stellen gezieltere Fragen. Das verbessert die Lernkurve und erhöht die Chancen, Fachkräfte langfristig zu binden.
Ein weiterer Effekt: Wenn gute Ausrüstung verfügbar ist, sinkt die Bereitschaft zu Improvisation – und damit das Risiko für Unfälle oder beschädigte Werkstoffe. Statt mit „irgendwas“ zu arbeiten, greifen Mitarbeitende lieber zum passenden Werkzeug. Das wiederum erleichtert die Einhaltung von Arbeitsschutzvorgaben – ganz ohne erhobenen Zeigefinger.
Warum lohnt sich eine Werkzeugstrategie über das Tagesgeschäft hinaus?
Viele Investitionsentscheidungen im Handwerk entstehen ad hoc – weil etwas kaputtgeht, weil ein Auftrag eine neue Maschine verlangt oder weil ein Mitarbeiter darauf hinweist, dass „das alte Ding“ nicht mehr zu gebrauchen sei. Doch der Blick über das Tagesgeschäft hinaus kann sich lohnen: Eine mittel- bis langfristige Ausrüstungsstrategie senkt nicht nur Kosten, sondern schafft Verlässlichkeit.
Das beginnt bei der Planbarkeit von Neuanschaffungen – etwa in Form jährlicher Technikbudgets. Auch Leih- oder Mietmodelle lassen sich in einer strategischen Herangehensweise besser einbinden. Viele Hersteller bieten heute Mietsysteme für Maschinen mit kurzer Einsatzdauer – inklusive Versicherung, Wartung und Service. Das spart Platz, Kapitalbindung und reduziert Verwaltungsaufwand.
Darüber hinaus lassen sich durch geplante Investitionen auch Abschreibungen steuerlich optimieren. Wer Werkzeuge nicht punktuell, sondern systematisch erneuert, kann die Kosten über mehrere Jahre verteilen und gleichzeitig von Förderprogrammen profitieren.
Auch im Hinblick auf die Außendarstellung ist eine klar erkennbare Ausstattungspolitik vorteilhaft. Betriebe, die auf einen einheitlichen Maschinenpark setzen, wirken strukturierter – nicht nur bei Kunden, sondern auch auf neue Mitarbeitende oder Kooperationspartner.
Welche Zukunftstrends bringen 2026+ noch mehr Effizienz?
Wer sich heute mit moderner Ausrüstung beschäftigt, stellt schnell fest: Die Entwicklung ist noch lange nicht abgeschlossen. Hersteller und Anwender denken längst in Plattformen, Schnittstellen und Datenmodellen. Dabei geht es nicht mehr nur um mechanische Leistung, sondern um ganzheitliche Systeme.
Ein Beispiel: In Zukunft werden sich Maschinen selbst melden, wenn Verschleißteile ersetzt werden müssen. Sensorik wird Wartungsintervalle vorausschauend planen – nicht erst dann, wenn es zu spät ist. Apps werden anzeigen, wo sich welche Maschine befindet, wie sie genutzt wurde und wann sie das letzte Mal geladen wurde. Das reduziert Stillstand und schafft eine neue Transparenz.
Weniger Geräte bedeutet weniger Aufwand
Auch im Bereich der Stromversorgung tut sich einiges. Akku-Plattformen mehrerer Hersteller wachsen zusammen, Adapterlösungen werden überflüssig. Das bedeutet: weniger Geräte, weniger Ladegeräte, weniger Aufwand. Parallel gewinnen nachhaltige Konzepte an Bedeutung. Einige Marken setzen schon heute auf recycelbare Gehäusematerialien, langlebige Komponenten und Rücknahmeprogramme für Altgeräte.
Doch nicht nur die Technik verändert sich. Auch das Handwerk selbst wird digitaler, mobiler – und internationaler. Schulungen finden per Video statt, Montageanleitungen per QR-Code. Das wirkt sich auf Anforderungen an Geräte genauso aus wie auf die Art, wie Werkzeuge ausgewählt und genutzt werden.
Wer seine Ausstattung regelmäßig auf dem neuesten Stand hält, bleibt also nicht nur effizient – sondern auch anschlussfähig an künftige Entwicklungen.
Fazit: Drei Schritte zur besseren Ausrüstung – mit System statt Zufall
Wer heute Projekte zuverlässig, schnell und sicher umsetzen will, braucht mehr als gutes Personal und Planung. Die Ausrüstung spielt eine zentrale Rolle – und sie verdient denselben strategischen Blick wie Materialbeschaffung oder Kundenakquise.
- Der erste Schritt: Eine ehrliche Bestandsaufnahme. Welche Werkzeuge sind in täglichem Einsatz, wo gibt es wiederkehrende Probleme? Gerade bei Geräten wie Trennschleifern, Sägen oder Bohrhämmern lohnt es sich, auch auf Aspekte wie Gewicht, Ergonomie und Energiebedarf zu achten.
- Im zweiten Schritt sollte priorisiert werden: Was hat den größten Hebel für den Alltag? Sind es bessere Akkus, eine neue Werkbank oder ein System zur Staubabsaugung? Nicht alles muss sofort ersetzt werden – aber wer gezielt investiert, spürt den Unterschied oft schon nach wenigen Tagen und kann überflüssiges Equipment mit einem gründlichen Frühjahrsputz aussortieren.
- Und drittens: Fördermöglichkeiten prüfen und mitdenken. Ob über die BG BAU oder andere Programme – wer sich hier rechtzeitig informiert, kann einen Großteil der Kosten abfedern. Das macht auch Investitionen in höherwertige Modelle planbarer.
Am Ende steht keine vollautomatische Baustelle – aber ein Arbeitsumfeld, das flüssiger läuft, gesünder ist und langfristig wettbewerbsfähig bleibt.